Back At It
Okay, it's been a while. It's now February 2003. But in the meantime I have spent a number of weeks out of town for work, I have ripped the bathroom out to the studs and put it back together, and I have gotten the jetski running and
out on the water. My contract work ended last week, so I decided to take the opportunity to get the jet boat finished.
Let's Get Ready to Rumble
When last I touched it, I was trying to get the impeller off. I pulled the jet pump out from behind the workbench. Nope, the impeller hadn't fallen off while
it was sitting there.
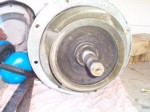
The last time I had seen the puller I had just broken off one of its legs. I pulled out the various peices of the puller and inspected it. Didn't look too bad. I cleaned off the surfaces with
the 4 1/2" angle grinder. I fired up the tig welder and put the leg back on, and added some braces to make the puller stiffer. Now it looked like something that could pull off an
impeller.
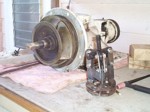
I got it hooked up to the jet pump and commenced to screwing down the central screw. A big breaker bar and cheater pipe on the screw, and a big pipe wrench and pipe on the puller helped exert
plenty of force.
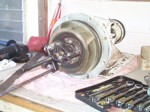
A little too much force, actually, because there was suddenly a loud ping and one of the welds broke. It was an older weld, probably from the time I tried to use the CO2 bottle from the mig
when the tig's argon bottle ran out on a Sunday afternoon. I still haven't gotten very good with my camera's closeup mode, but you can kind of see the crack at the base of the leg.
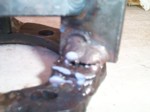
I took the puller back off the pump, cleaned everything up with the grinder, and welded it back together. I also added one more little brace where the puller tended to bend. I put everything
back together and put in on the pump, and began to crank the center screw again. It looked like I had finally gotten everything right, because no matter how hard I cranked it down the puller
would not break. Of course, the impeller wouldn't come off either. I got out the torch, which was really low on O2, but figured I would try it anyway. I got a lousy flame, and put a thick
coating of soot on the impeller and puller. I didn't seem to be getting much heat into the impeller, and it was getting dark, so I called it a day.
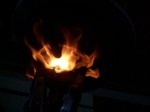
A New Beginning
I considered elaborate plans for making up another puller, but I really wanted to get this done with the least amount of effort. Then I remembered I had bought a power
puller a couple months ago from Harbor Freight. It was on sale for $63, and I just couldn't pass it up. I didn't know quite what I was going to do with it when I got it, but I had to have it.
And here was the perfect use! I could replace the turnscrew with the power of hydraulics.
The next morning I called my friend Allen Rose, who had done the original machining for the rings on the puller. I asked him if we could use his drill press to put holes in some mild steel
strap, to lengthen the puller so the hydraulic ram from the power puller kit would fit into the puller. I picked up nine feet of 1x0.25" stock at Home
Despot on the way to Allen's house, and we got the holes drilled quickly. Back at home, I assembled everything. It went together perfectly (after a little grinding).
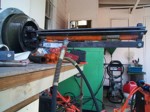
I began pumping. The ram quickly took up the slack, and it got hard to pump. Soon I was standing on the pump handle to get it to move. I figured that meant I shouldn't pump any more. But the
impeller still hadn't moved. Okay. I went to the welding supply store (just a mile away) and got fresh oxygen and acetylene cylinders. I took the pressure off the ram and fired up the torch.
This time I used a big tip (#7 Meco Jet Aviator Torch) and really turned the flame up. I spent 15 minutes moving the torch around the impeller hub, really putting the heat in. Finally I
killed the torch, positioned the ram, and started pumping. And the impeller moved!
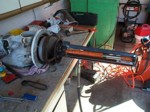
It didn't want to come, and it groaned every time it moved. But I got it off pretty quickly. It was the first time I had gotten a good look at the impeller.

The shaft had some powdery white corrosion on it. Or it could have been locktite. And the wear ring didn't look too bad. But something had been causing the jet pump to behave like an
automatic transmission with no fluid in it.
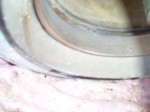
That was nice to finally get it off. The wear ring was damaged by the heat, as I expected, so it will have to come out, which means I have to replace it. That means I have to either measure
my impeller, and determine what size wear ring to order, or send the impeller off to be worked on and matched to a wear ring. That is probably the easiest route.
I also have to stop by the storage yard and pay a couple more months rent on the boat. I went by last month to check on it, and it looked okay, with the exception of a mangled trailer tongue
from the new yard owners moving it around. And they promised they would replace it. I hope the engine is not in too bad a shape. I never intended to leave it for eight months the last time I
parked it.
Soon, very soon the boat will be back together, throbbing with the power of 455 cubic inches. Soon, I tell you.